Warehouse occupancy costs are a necessary part of doing business. If you have goods to move, ship or fulfill, you need space to store and handle those goods. However, applying good strategies to your warehousing can significantly lower your overall occupancy cost:
1. Know Your Market
The first step in managing your warehouse occupancy costs is to understand what space costs in the surrounding market. If your expenses per square foot are above the market's norm, you may not have to change a great deal about how you use your warehouse.
Instead, you may be able to achieve cost reductions by sitting down with your landlord, explaining market reality and having your rent adjusted to what it would be if you moved out and he had to spend tens or hundreds of thousands of dollars to find a new tenant. Researching both asking rents and recently signed leases as well as the new construction market is a key part of leveraging this strategy.
2. Leverage Public Warehousing Wisely
While public warehousing services can be expensive and may even unwieldy at times, it also has a key benefit. If you're able to use someone else's space during times when your warehouse space demand spikes, you can carry less space and lower your warehouse occupancy costs across the board. Working out a relationship with a public warehousing provider that will ensure your ability to lease space when you need it will help to mitigate some of the seasonal availability issues that impact some markets.
3. Measure Your Utilization
Measuring your utilization rate solves two problems. First, if you have significant empty space in a warehouse, you can easily identify it as a candidate to be cut back when its lease rolls. However, low utilization rates for a warehouse that you are actively using could be a sign of warehouse management issues or an ineffective layout. If your warehouse utilization percentage isn't in the low 20s, there might be a problem. After all, squeezing more effectiveness out of each square foot effectively lowers your warehouse occupancy costs.
Use our FREE Warehouse Utilization Calculator
4. Focus on The Right Space Measurement
If you have large items that can be effectively stacked on very tall racks, a high clear height warehouse may be appropriate for you. Clear heights north of 40 feet are common and some warehouses are now being built to accommodate more than 50 feet of vertical storage. While their rents per square foot may be high, the rents per cubic foot can be very affordable.
Not every product is appropriate for this type of storage. If your business fulfills small items out of its warehouse, the clear height becomes less important and getting enough floor area is a more important metric. In these instances, you can control your warehouse occupancy costs by considering older buildings with lower clear heights and lower rents. They're less desirable to other tenants, but perfect for you.
5. Rethink Roles
Your most expensive space might actually be your least expensive warehouse. Some e-retail operations are turning their retail inventories over to their dot-com divisions, letting Internet orders pick from retail stores. With this in mind, the relationship between stores and warehouses is shifting. If you can better utilize your store space to hold goods for sale in either traditional or online channels, you may be able to reduce your warehouse occupancy costs by reducing your warehouse space.Helping you save on your real estate is what we do.
Here are a few other articles we know you'll enjoy:
Commercial Warehouse Touring Tips
Five Practices for a Great Property Tour
Seven Must Haves for Your Warehouse Space
Subscribe to our blog for more CRE tips!!
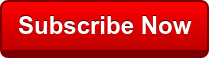