Once you have warehouse space, you might be surprised at how quickly you can fill it up. When your warehouse is full, the easy solution is to go out and lease more space. However, before you commit to boosting your occupancy costs, you can probably squeeze more efficiency out of your existing storage facilities. Here are some general problems, and some ways to fix them.
Problem: Too Much of the Wrong Stuff
One of the challenges inherent in warehousing is that some items come in and don't ever leave. Storing the wrong SKUs in your warehouse space is expensive in two ways. First, you are wasting expensive space that you can use more productively. Second, the longer you hold onto obsolete items, the less valuable they become (to the extent that they have any value left now).
Solving this problem is simple. Get the unused items out of your warehouse. Usually, the challenge in doing this has nothing to do with warehouse operations. Instead, it's financial. However, once you decide to take the hit on either selling those items for their true market value or simply disposing them and writing them off, you will be better positioned for future profit.
Use our FREE Warehouse Optimization Calculator
Problem: Too Much of the Right Stuff
Your warehouse can also be full because you are overstocking popular items. This isn't always a bad thing. Ultimately, if you have short-term spikes in demand, it might make good sense to simply put up with having your warehouse overstuffed for a couple of weeks a year. If this is a constant problem, though, you may need to make some changes.
The easiest solution is to push the need to store those items away from the warehouse space that is being over-utilized. This could mean having the manufacturer or distributor hold onto the items and ship them out using faster means of freight on an as-needed basis. Another option, if you sell direct to the consumer, is to work with your sources to move to a drop shipping model where you do not have to store them at all. If you operate retail outlets, you could also shift more merchandise to stores, requiring them to find places to store it.
Problem: Unutilized Warehouse Space
Look carefully at your warehouse space and at the surrounding areas. Reconfiguring the space is another blog topic in and of itself. However, you might have some low-hanging fruit for expanding your warehouse right outside. If your warehouse has unused yard space, outdoor storage could be an option. With some items in some climate zones, simply placing them in a fenced area could be enough. In others, you could need to rent containers or leave the items on truck trailers. While this option is expensive, it could be much less expensive than leasing new space.
A similar solution is to utilize someone else's warehouse space to store your overflow. Typically, this option works well when you have a short term need and it works best when your short-term need corresponds with someone else's reduced utilization. For instance, if your company makes patio furniture, it could occupy the spring and summertime space in a warehouse that stores holiday decorations in fall and winter. As with renting containers, this is usually much more expensive on a per square foot basis than leasing space, but short term usage could balance this cost out.
Warehouse articles to take a look at:
High Tech Warehouse Innovations
Top Warehouse Space Trends of 2016
Seven Must Haves for Your Warehouse Space
Subscribe to our blog for more CRE tips!
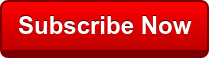