In this article, you'll learn:
- How to measure your warehouse's usable and storage capacity.
- The process for calculating your inventory cube size and utilization rate.
- Why a 15% utilization rate is generally acceptable.
- The impact of warehouse design on storage efficiency and labor costs.
Most warehouse managers report that their biggest problem is that they do not have enough space. Yet, many warehouses operate with just 20 percent of their space being used at any time. Furthermore, some warehouses that have higher utilization rates end up with higher costs due to the negative impacts of high utilization on employee productivity.
Calculating utilization is a relatively simple process which starts with calculating the size of your warehouse. Measure the total floor area of the warehouse, then subtract out any space that is occupied with offices, restrooms or other non-storage related space. For example, if you have a 300 foot wide and 200 foot long warehouse with 5,000 square feet of office space, you effectively have a 55,000 usable square foot warehouse. Multiply that number by the building's clear height to find its storage capacity in cubic feet. If this building had a 27 foot clear height, its storage capacity, or cube size, would be 1,485,000 cubic feet.
To find your utilization, you need to calculate your inventory cube size. To do this, add up the volume of all of the products that you store in your warehouse, and divide that sum by the building's storage capacity. If you have 225,000 cubic feet of product in your 1,485,000 cubic foot warehouse, you have 15.15 percent utilization, which is relatively healthy.
To understand why 15 percent utilization is actually not that bad, take a step backwards and calculate the size of the storage cube in your warehouse. To calculate this, measure the footprints of each of your pallet racks and measure their total vertical storage capacity. Once you have calculated the true capacity of each rack, multiply it by the number of racks in your warehouse to find the size of the storage cube. Most warehouse storage cubes are between 22 and 27 percent of their storage capacities. With a 1,485,000 cubic foot warehouse, a storage cube of 326,700 and 400,950 square feet would be normal.
In most cases, storage cube sizes outside of the 22 to 27 percent range indicate a problem in your warehouse's design. If the storage cube size is smaller, you might be wasting space by not locating racks as efficiently as possible. If your storage cube size is larger, you run the risk of inflated labor costs due to your employees not having enough room to efficiently move around the warehouse for picking and restocking.
Comparing your inventory cube to your warehouse's cube size gives a low number that reflects both on your utilization of your space and on the choices you made in designing your warehouse. Once you have optimized your warehouse design, calculating the utilization of your storage cube by dividing it into the inventory cube can give you a more exact indication of your efficiency. Taking the midpoint of the above example and assuming that the warehouse has a 363,825 storage cube, storing 225,000 cubic feet of product would 61.84 percent utilization of the available storage space.
When you evaluate your warehouse, choose your metrics based on what you are trying to accomplish. Comparing inventory to building size is a popular utilization metric, but does not always help you understand what is going on in your building. The two-step model outlined here helps you understand how your warehouse's overall design interfaces with how your employees use it on a day-to-day basis.
Here are a few other article we know you'll enjoy:
How Much Does a Tenant Rep Cost?
Subscribe to our blog for more CRE Tips!!
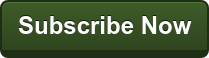
Wondering where to begin?
Related Content
- 6 Metrics That Matter With Industrial Buildings
- What Drives Up Warehouse Operating Costs? The 4 Most Common Mistakes To Avoid
- The Ultimate Warehouse Checklist for Corporate Tenants
- Leasing Warehouse Space? Here's Your Top Considerations as a Tenant